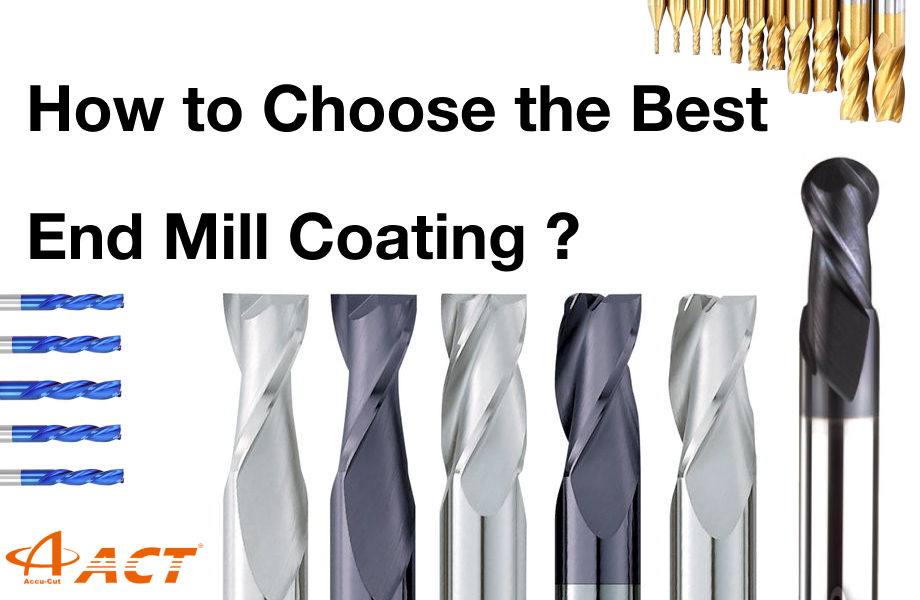
What is End Mill Coating?
End mill coatings are protective layers applied to cutting tools, much like how different clothes protect you from various weather conditions.
The right coating can dramatically improve the performance of the tool, extending its lifespan and making it more efficient.
There are two main types of end mill coatings, based on how they're applied:
- Physical Vapor Deposition (PVD): Thin, hard coatings ideal for tools that don't reach high temperatures, like high-speed steel. Examples include TiN, TiCN, and CrN, which provide precision and sharpness.
- Chemical Vapor Deposition (CVD): Applied at higher temperatures, suitable for tools used in extreme heat. Examples include AlTiN and ZrN, perfect for machining hard metals like stainless steel or titanium.
Benefits of Coatings in End Mills
Coatings provide key benefits that enhance end mill performance:
- Extend Tool Life: Coatings help tools stay sharp longer, reducing the need for frequent replacements and improving cost-efficiency.
- Improve Precision: By increasing lubricity and reducing friction, coatings result in more accurate cuts and a better surface finish.
- Higher Cutting Speed: Coated tools can operate at higher speeds without losing efficiency due to improved heat resistance.
- Better Chip Evacuation: Coatings like TiCN aid in smoother chip removal, reducing the risk of tool and workpiece damage.
Risks of Choosing the Wrong End Mill Coating
Selecting the wrong coating can negatively affect your machining process, leading to:
- Increased Tool Wear: Coatings not suited for high temperatures or abrasive materials wear out quickly, exposing the tool, eventually leading to chipping.
- Poor Surface Finish: Mismatched coatings increase friction, resulting in rougher cuts and a lower-quality surface finish.
- Overheating: Coatings lacking proper heat resistance may lead to overheating, damaging both the tool and the workpiece.
Common end mill coating types and what are they best for?
End mill coating chart
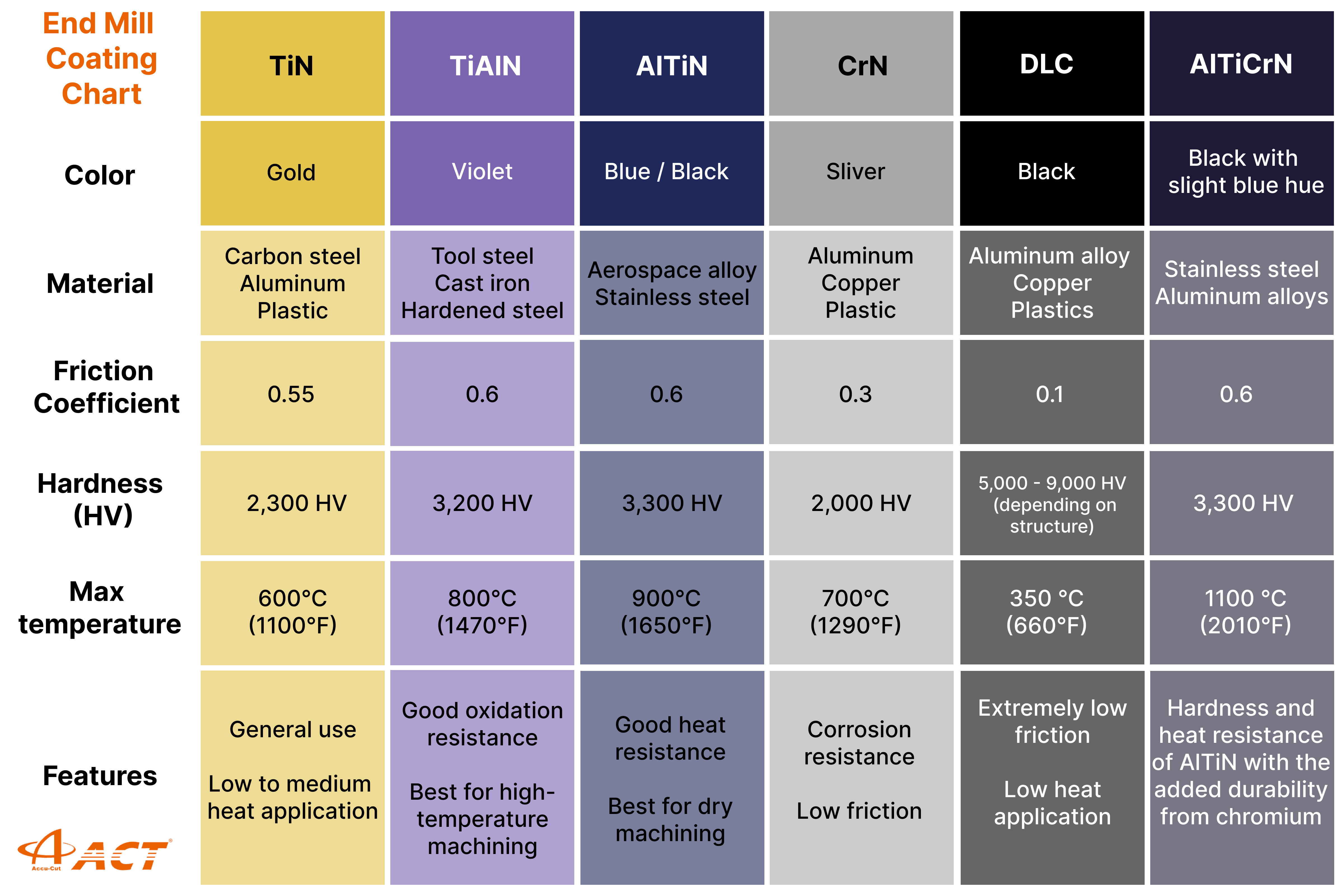
1. TiN (Titanium Nitride) Coating
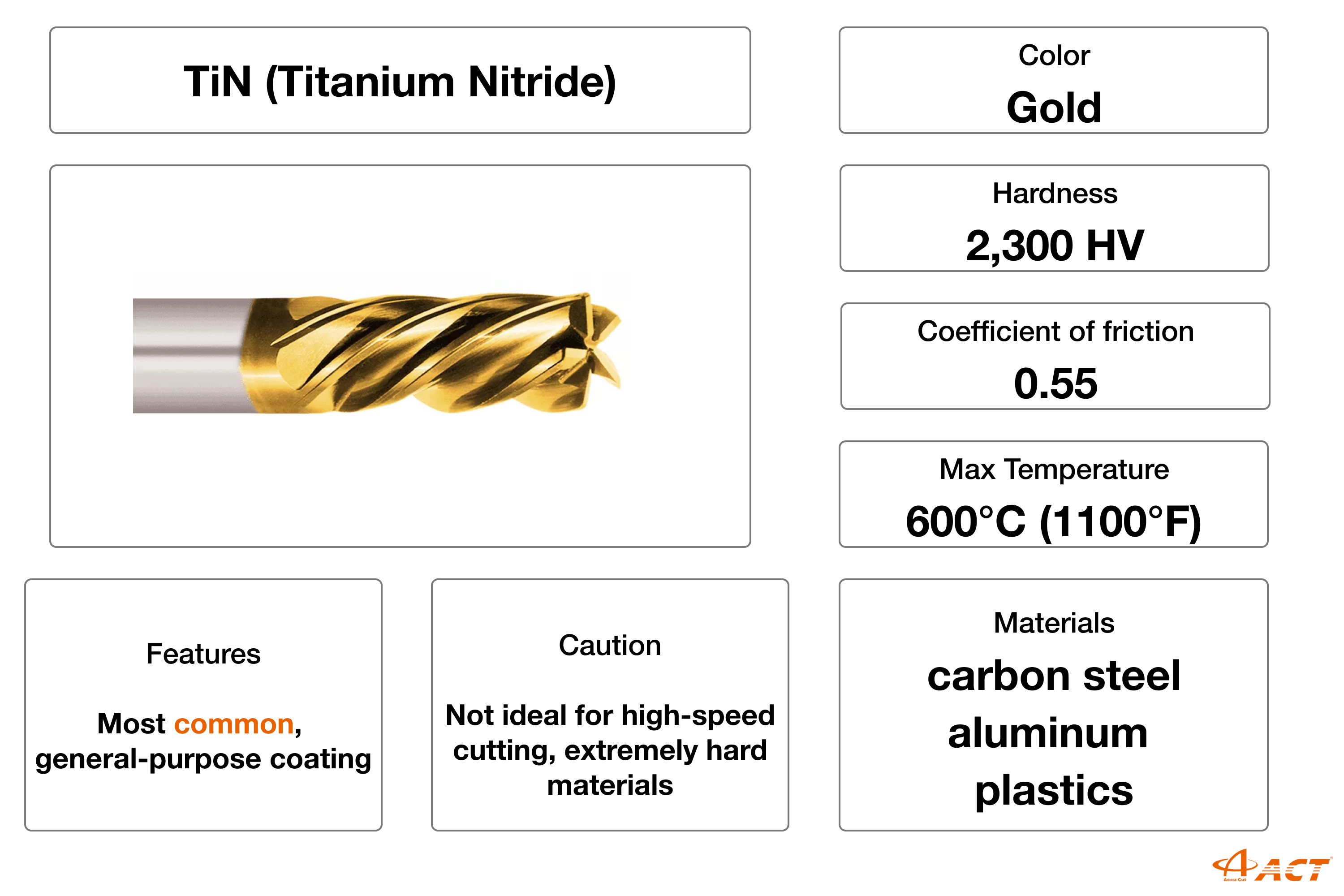
- Hardness: ~ 2,300 HV.
- Max operating temperature: ~ 600°C (1100°F).
- Coating color: Gold.
- Is titanium nitride coating good?
- Most common, general-purpose coating with moderate wear resistance.
- Suitable for low to medium heat applications.
- Enhances tool life in everyday cutting tasks.
- What is TiN caoting good for? Cutting softer materials like carbon steel, aluminum, and plastics at low to medium speeds.
- What are the disadvantages of titanium nitride?
- Not ideal for high-speed cutting or extremely hard materials like hardened steel. Might flake or chip.
2. TiAlN (Titanium Aluminum Nitride) Coating
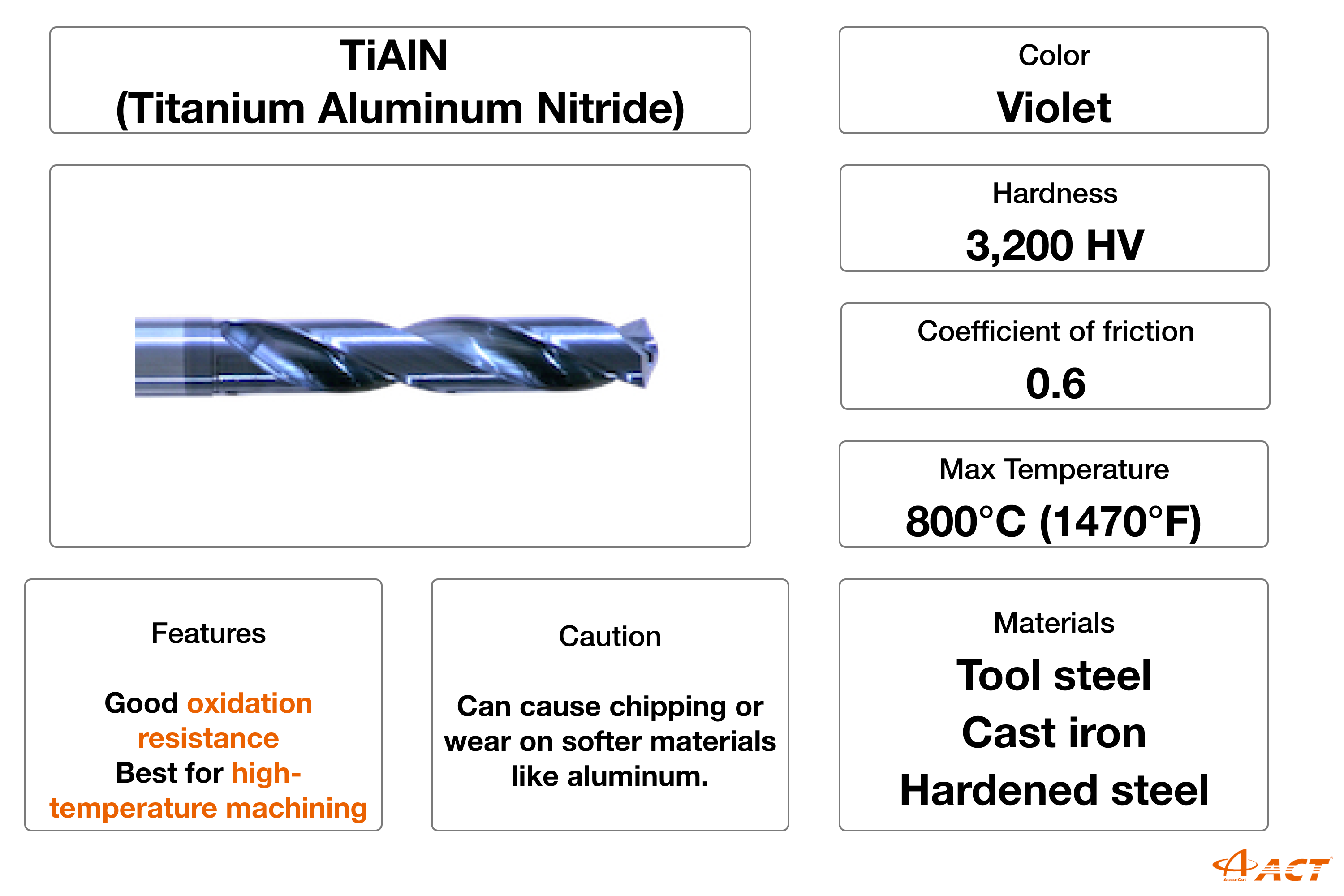
- Hardness: ~ 3,200 HV.
- Max operating temperature: ~ 800°C (1470°F).
- Coating color: Violet.
- Features:
- Provides excellent oxidation resistance, making it ideal for high-speed machining.
- Forms a protective aluminum oxide layer at high temperatures, significantly reducing tool wear and extending tool life.
- Superior heat resistance allows it to perform well in dry machining.
- What is TiAlN coating good for?
- Hard materials such as tool steel, cast iron, and hardened steel (40-55 HRC).
- High-speed cutting tasks, particularly in dry conditions.
- Caution:
- Can cause chipping or wear on softer materials like aluminum.
- Excessive coolant can prevent the protective layer from forming, reducing its benefits.
3. AlTiN (Aluminum Titanium Nitride) Coating
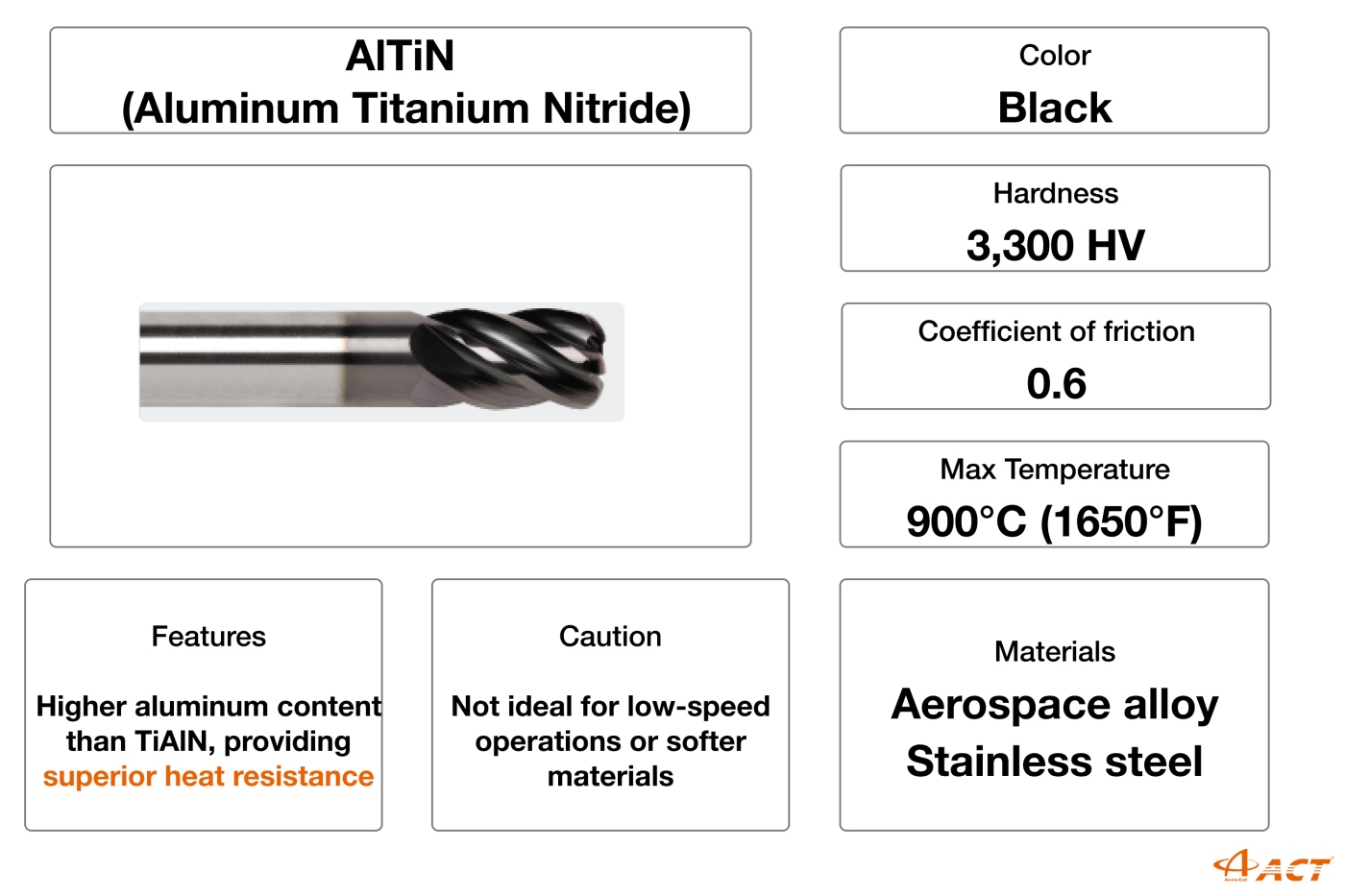
- Hardness: ~ 3,300 HV.
- Max operating temperature: ~ 900°C (1650°F).
- Coating color: Black.
- Features:
- Higher aluminum content than TiAlN, providing superior heat resistance.
- Excellent wear protection for high-temperature cutting operations.
- What is AlTiN coating good for?
- Hard materials (up to 60 HRC), aerospace alloys, and stainless steel.
- Performs well in dry machining, reducing the need for coolant.
- Caution:
- Not ideal for low-speed operations or softer materials, as it needs high temperatures to activate its protective properties.
4. CrN (Chromium Nitride) Coating
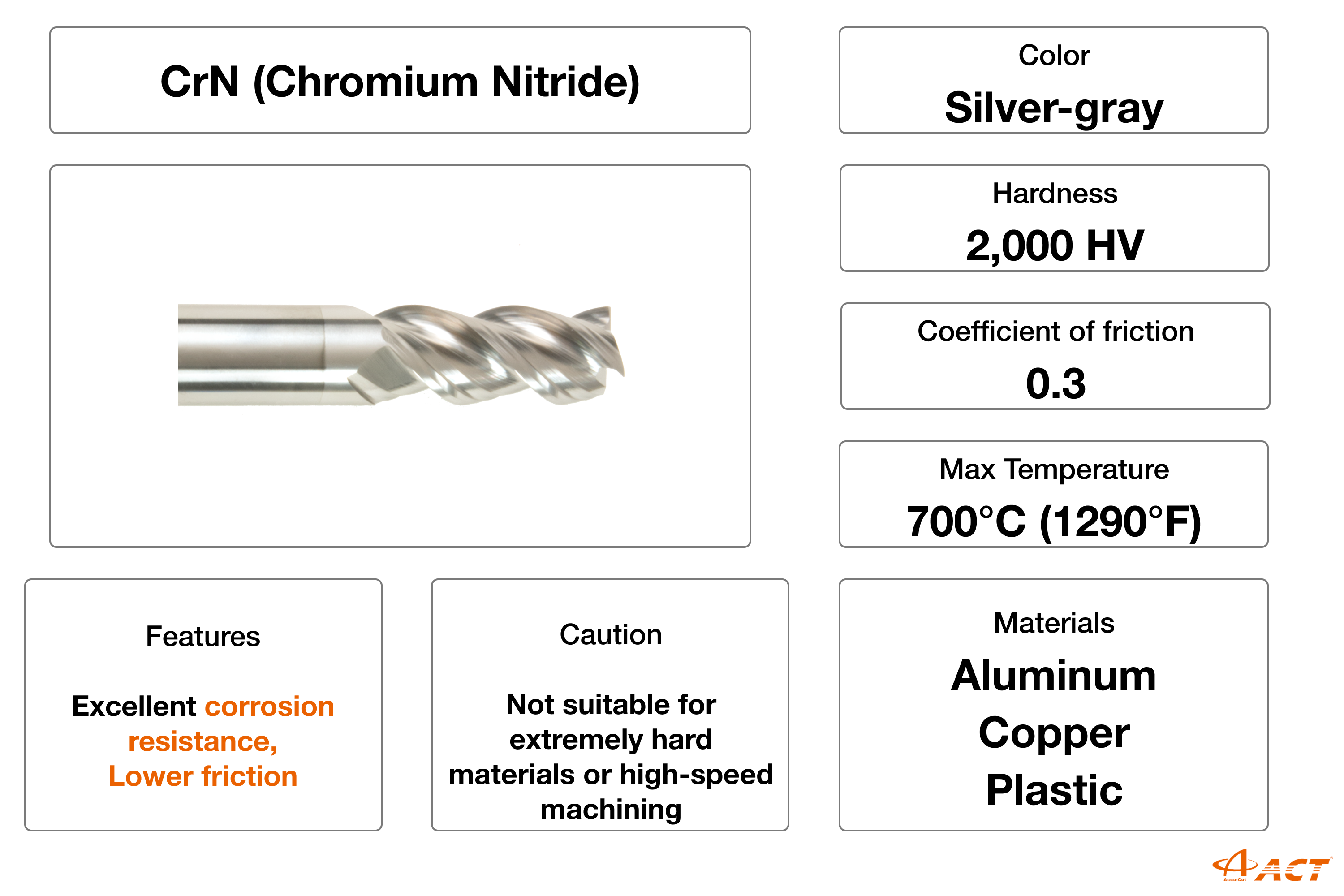
- Hardness: ~ 2,000 HV.
- Max operating temperature: ~ 700°C (1290°F).
- Coating color: Silver-gray.
- What are the benefits of CrN coating?
- High corrosion resistance, ideal for humid or abrasive environments.
- Lower friction compared to TiN, making it effective for softer or sticky materials.
- What is CrN coating good for?
- Aluminum, copper, and plastic, especially in conditions where corrosion is a concern.
- Caution:
- Not suitable for extremely hard materials or high-speed machining, as it lacks heat resistance.
5. DLC (Diamond-Like Carbon) Coating
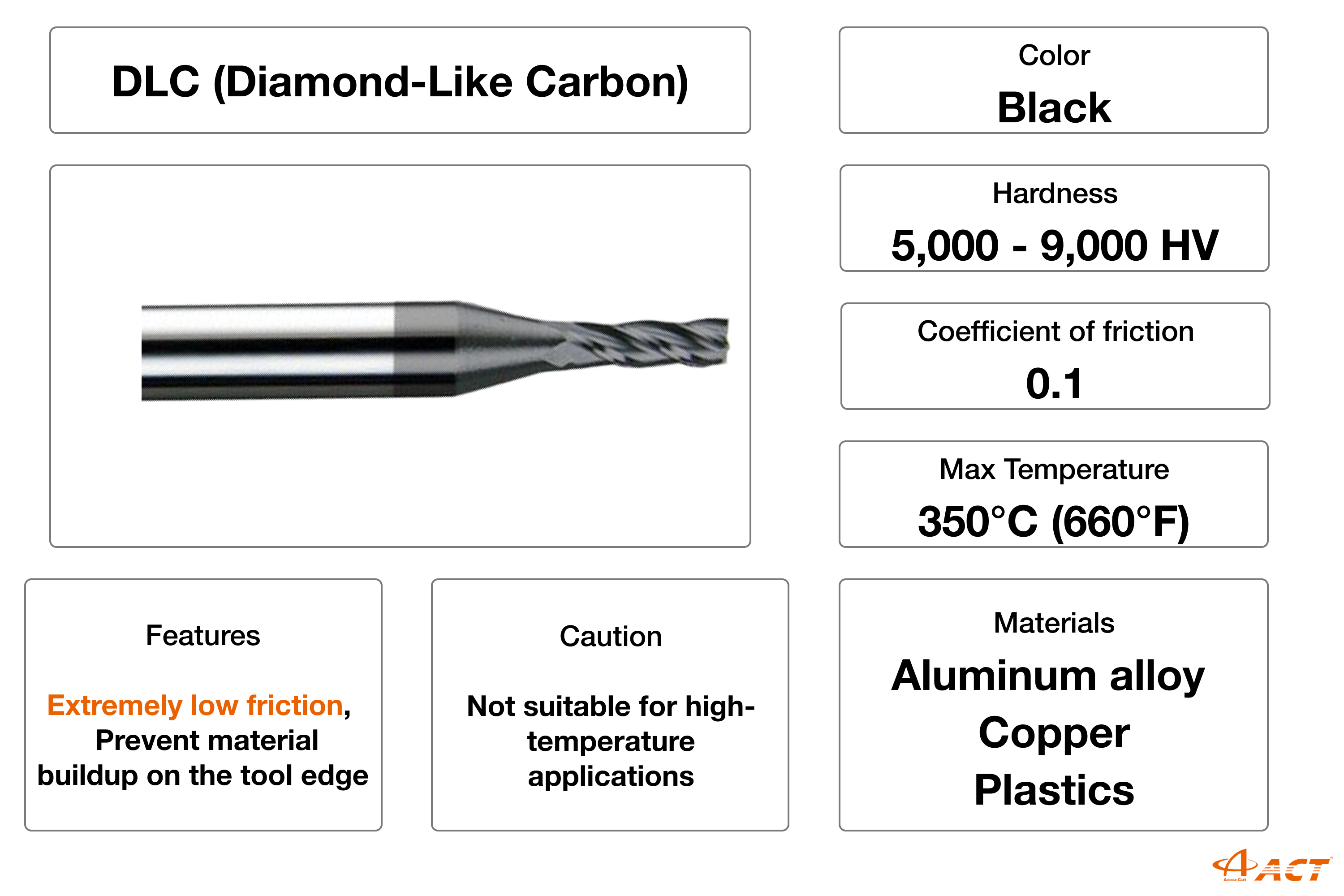
- Hardness: ~ 5,000 - 9,000 HV (depending on structure).
- Max operating temperature: ~ 350°C (660°F).
- Coating color: Shiny mirror-like black.
- Features of DLC coating:
- Extremely low friction, similar to natural diamond.
- Highly effective at preventing material buildup on the tool edge, improving tool longevity.
- Excellent for machining non-ferrous and soft metals.
- What is DLC coating good for?
- Aluminum alloys, copper, and plastics, particularly in applications where preventing material adhesion is critical.
- What are the disadvantages of diamond-like carbon?
- Not suitable for high-temperature applications, as it lacks the heat resistance of other coatings like AlTiN or TiAlN.
6. AlTiCrN (Aluminum Titanium Chromium Nitride) Coating
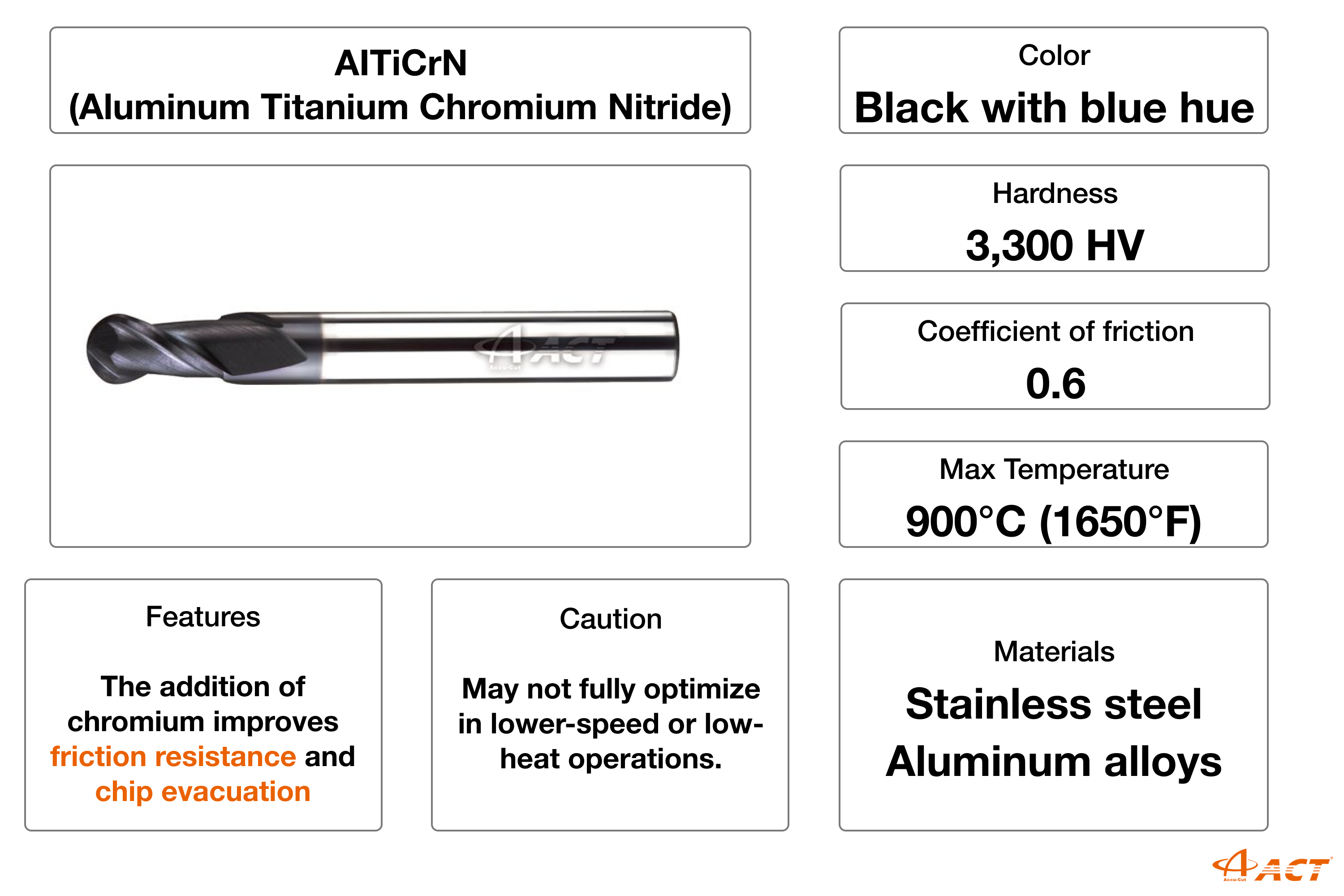
- Hardness: ~ 3,300 HV.
- Max Operating Temperature: ~ 1100°C (2010°F).
- Coating Color: Black with slight blue or purple hue.
- Features of AlTiCrN coating:
- Better Lubricity & Chip Evacuation: Chromium addition enhances friction resistance and chip flow, improving efficiency and tool life in high-performance machining.
- Strong Wear Resistance :Combines the hardness and heat resistance of AlTiN with chromium’s added durability, making it ideal for challenging cutting tasks.
- High Oxidation & Thermal Stability: Withstands up to 1,100°C, ideal for high-speed cutting and dry machining.
- What is AlTiCrN coating good for?
- Hard materials, stainless steel, aluminum alloys, and applications requiring high temperature resistance and effective chip removal.
- Caution:
- Its performance may diminish at lower speeds or cooler temperatures.
How to Identify a End Mill Coating Type
It can be challenging to identify a coating type by color alone.
Although AlTiCrN is a common black coating, other coatings like AlTiN, TiAlN, TiCN, CrN, and DLC also appear in black or dark gray hues.
Here are some reliable methods for distinguishing between coatings:
- Surface Gloss:
- AlTiCrN: Often metallic black with slight blue or purple hues.
- AlTiN / TiAlN: Matte black or bluish-gray with a subdued finish.
- DLC: Shiny, mirror-like black due to its smooth carbon structure.
- Temperature Resistance:
- AlTiCrN and AlTiN: Stable up to 1,100°C, ideal for high-speed, dry cutting.
- TiAlN: Begins to oxidize around 800°C, offering moderate high-temperature resistance.
- Hardness and Wear Resistance:
- TiCN: Harder than TiN but less suitable for high-temperature applications.
- AlTiCrN and AlTiN: High hardness and heat resistance, making them suitable for prolonged machining.
- Corrosion Resistance:
- CrN and DLC: Excel in corrosion resistance, particularly for medical or food-grade applications.
- AlTiCrN: Offers good corrosion resistance, optimized for wear and cutting.
- Friction Coefficient:
- DLC: Extremely low friction, ideal for precision tools like surgical instruments or automotive parts.
- AlTiCrN and AlTiN: Moderate friction, effectively reducing wear during cutting.
- Chemical Testing or Spectral Analysis:
For precise identification, use X-ray fluorescence (XRF) or energy-dispersive X-ray spectroscopy (EDS) to analyze elements in the coating, such as chromium in AlTiCrN. Consulting suppliers can also ensure the coating meets specific application needs.
End mill coating FAQs
1. What is the best end mill coating for stainless steel?
Coatings like AlTiN (Aluminum Titanium Nitride) are great choices for stainless steel. These coatings handle the high heat generated when cutting stainless steel and provide excellent wear resistance. Avoid using coatings that aren't heat-resistant, as stainless steel generates a lot of friction.
2. What is the best end mill for aluminum?
The best end mill for aluminum are DLC (Diamond-Like Carbon) or CrN (Chromium Nitride) coating. These coatings provide low friction, excellent wear resistance, and help prevent material buildup on the tool edge.
3. Why even use uncoated mills?
Uncoated end mills are budget-friendly, versatile, and suitable for a range of materials, including aluminum and stainless steel. However, they may wear faster and are less suited for high-speed or high-temperature applications compared to coated tools.
4. What is the difference between TiAlN coating and AlTiN coating?
The main difference is aluminum content.
AlTiN has more aluminum (greater than 50%), making it better for high-temperature applications due to its superior oxidation resistance. TiAlN, with less aluminum (50% or less) , offers higher hardness and lower friction, ideal for medium heat and tough cutting conditions.
5. What is the best coating for cutting titanium?
AlTiCrN (Aluminum Titanium Chromium Nitride) is ideal for cutting titanium due to its high hardness and heat resistance. Check out the ACCU CUT store to learn more and find the best end mills with AlTiCrN coatings.