40460
No.90, sec. 2, Hwa Mei Str.,
Taichung, Taiwan.
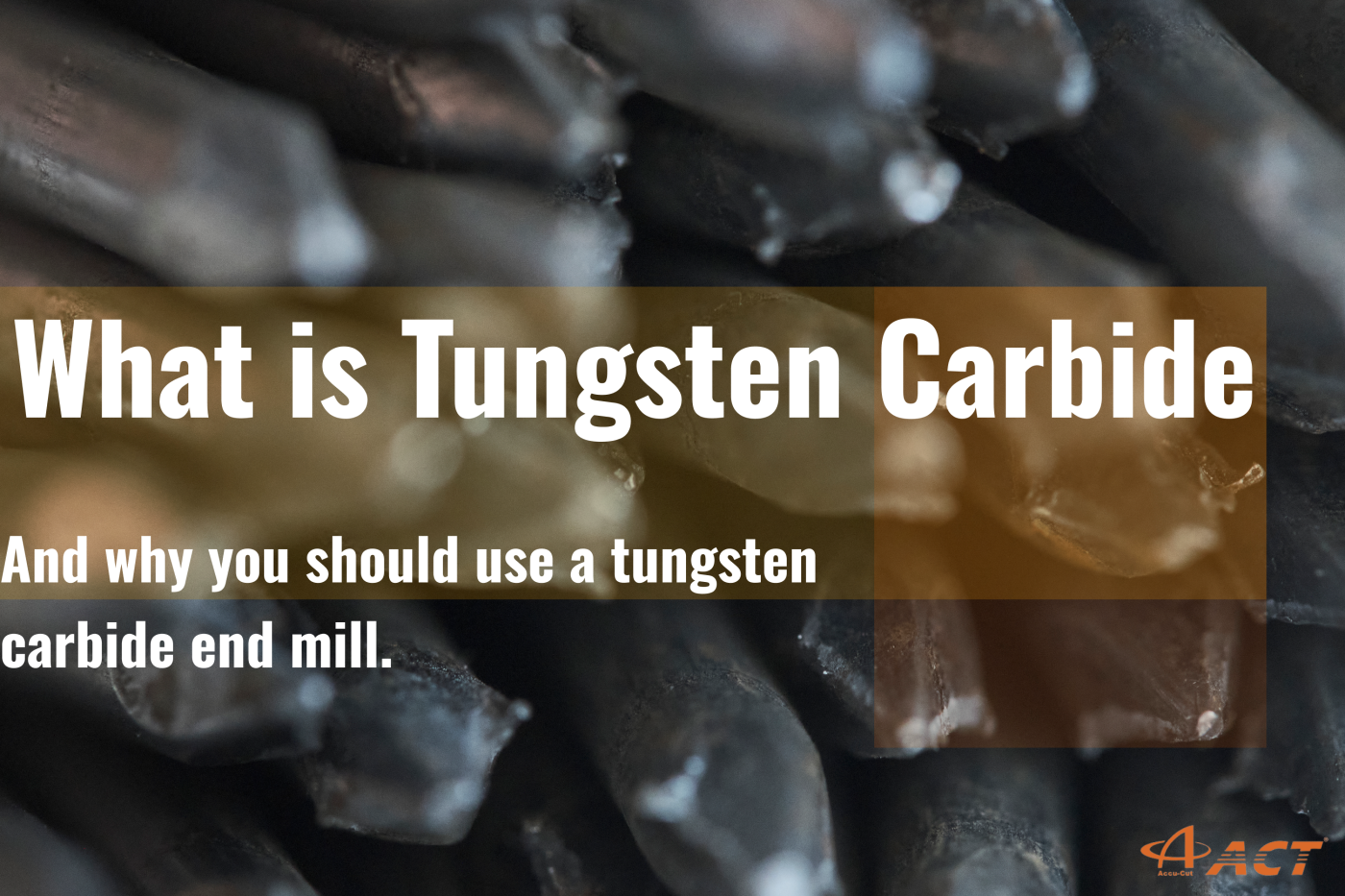
Still using High-Speed Steel endmills for your CNC machine? It's time to step up your game.
If you're serious about precision machining and tired of constantly replacing worn-out tools, tungsten carbide endmills are your answer.
In this article, we'll show you why these premium cutting tools are worth every penny - and why settling for anything less might be costing you more than you think.
What is tungsten carbide?
Tungsten carbide is an engineered material that combines tungsten metal with carbon atoms at the molecular level.
What is so special about tungsten carbide?
When tungsten is combined with carbon, its hardness increases dramatically, transforming it into one of the toughest materials available for industrial applications.
Key Characteristics of Tungsten Carbide:
- Extreme Hardness: 9.0 on the Mohs scale, comparable to sapphire and just below diamond.
- Wear Resistance: Maintains sharp edges and resists deformation under stress.
- Heat Resistance: High-temperature stability, withstands up to 2,870°C.
- Density: 15.6 g/cm³, heavier than steel but ideal for high-precision cutting tools.
Tungsten vs. Carbide vs. Tungsten Carbide
Material | Composition | Hardness (Mohs Scale) | Key Properties | Common Uses |
---|---|---|---|---|
Tungsten | Pure metal | 7.5 | High melting point, dense, ductile | Electrical filaments, aerospace, medical |
Carbide | Compound of carbon with a metal | Varies | Hard but brittle, chemically bonded | Ceramics, abrasives, coatings |
Tungsten Carbide | Tungsten + Carbon | 9.0 | Extremely hard, wear-resistant, heat-stable | Cutting tools, CNC machining, industrial wear parts |
High Speed Steel (HSS) vs. Solid Carbide End Mill
In CNC machining, the choice of endmill material directly impacts performance, tool life, and cost-efficiency. HSS and solid carbide (tungsten carbide) endmills are two of the most common options, but they serve different purposes.Why Tungsten Carbide is the Best Choice for CNC Endmills
Here's why tungsten carbide (solid carbide) excels HSS in CNC machining:- High Hardness & Wear Resistance → Maintains sharp cutting edges significantly longer than HSS
- Higher Cutting Speeds → Handles higher RPMs while maintaining edge integrity
- Stable Performance in Rigid Setups → Performs best in high-speed, high-precision operations with minimal vibration
- Reduced Tool Changes → Extended tool life results in fewer replacements and improved workflow efficiency
Common End Mill Materials Comparison
Material | Hardness | Toughness | Wear Resistance | Best for |
---|---|---|---|---|
HSS | Medium | High | Low | General-purpose cutting, manual mills |
Cobalt Steel | Higher than HSS | Moderate | Medium | Harder materials, extended HSS performance |
Powdered Metal | Medium-High | Moderate | Medium-High | Hybrid between HSS & carbide, better edge retention |
Solid Carbide | Very High | Low | Very High | High-speed CNC, precision machining |
Tips when using Tungsten Carbide Endmill
Tungsten carbide endmills are powerful tools, but they require proper handling. Their hardness gives them exceptional cutting ability, but their brittleness means they must be used correctly to avoid premature failure.4 Common Mistakes When Using Tungsten Carbide Endmills
1. Poor Cooling and Heat Management
Tungsten carbide can withstand high temperatures, but excessive heat leads to thermal fatigue and premature wear. Always use appropriate coolant or compressed air, especially when machining hard materials.2. Insufficient Machine Rigidity
Carbide endmills perform best in stable, vibration-free CNC setups. Weak machine rigidity or poor workpiece clamping can cause tool chatter, leading to chipping or tool failure.3. Overestimating Hardness
Many assume carbide’s high hardness makes it indestructible, but its brittleness means improper use can lead to cracking or chipping. Avoid aggressive cuts or excessive feed rates that could overstress the tool.4. Improper Regrinding Practices
While carbide endmills can be reground, each regrind alters the tool geometry, affecting cutting efficiency. Regrind only when necessary and ensure precision grinding to maintain performance.Use, Store, and Maintain Tungsten Carbide Endmills
1. Correct Usage
- Use on high-rigidity CNC machines to prevent vibrations.
- Maintain stable feeds and speeds—avoid sudden changes in cutting pressure.
- Use proper cooling to minimize thermal damage and extend tool life.
2. Storage Tips
- Store endmills in tool holders to prevent damage from contact.
- Keep in a dry environment to prevent carbide binder oxidation.
- After impact, inspect the tool for microfractures before use.
3. Cleaning and Maintenance
- Clean off cutting debris right after use to prevent material buildup.
- Clean with ultrasonic methods or soft brushes—avoid harsh scrubbing that can damage coatings.
- Before each use, inspect for edge dulling and micro-chipping.
What Materials Can Tungsten Carbide Endmills Cut?
Tungsten carbide endmills excel in cutting hard and abrasive materials that would wear down HSS quickly.Best Materials:
- Hardened Steel (45+ HRC) → Ideal for machining tough steels.
- Stainless Steel & Titanium → Excellent for aerospace and medical applications.
- Cast Iron & Tool Steels → Withstands abrasive wear in production machining.
- Composites & Carbon Fiber → Maintains sharpness in abrasive materials.
- Soft Aluminum & Plastics → Carbide may cause built-up edges, reducing cutting efficiency. Use uncoated or specialized carbide tools for these.
- Extremely High-Temperature Alloys → Requires advanced coatings and optimized cutting parameters.
Why Choose ACCU CUT Tungsten Carbide Endmills?
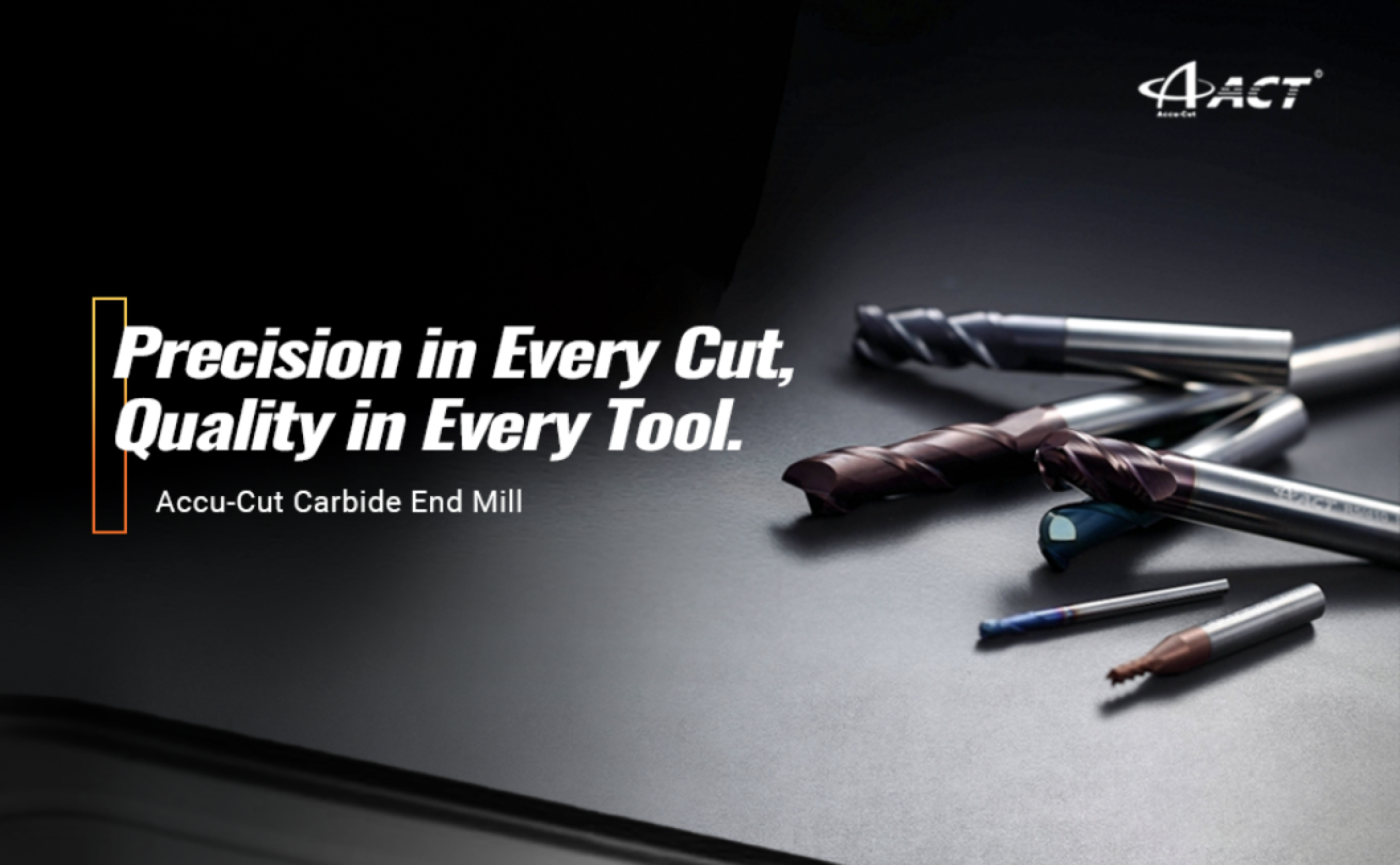
Built with cutting-edge technology and decades of expertise, every ACCU CUT endmill is crafted for machinists who demand nothing but the best.
But don't just take our word for it - let us show you why.
1. Precision Material Selection
Each endmill features ultra-fine grain tungsten carbide, precisely selected to achieve the optimal balance of hardness, toughness, and fracture resistance.Our material composition is refined through real-world machining data, ensuring maximum stability under high loads.
2. Advanced Coating Technology
We don't just apply any coating - we use advanced European-engineered coating processes that are customized for your specific needs.These aren't your average coatings - we're talking 3000+ HV hardness that delivers exceptional heat resistance, reduced friction, and minimal adhesion.
Your tools last longer, cut faster, and perform better - even when you're pushing the limits of high-speed machining.
3. Optimized Tool Geometry for Stability & Efficiency
We've engineered these tools to minimize vibration and maximize chip evacuation, because we understand that smooth operation is crucial for your success.This design means less force, zero deflection, and reliable performance even in your toughest jobs.
4. Industry-Leading Dimensional Accuracy
Our endmills don't just meet industry standards for roundness and straightness - they exceed them.Through 100% quality inspection before shipment, we guarantee complete uniformity and reliability.
Our tools achieve surface roughness as fine as Ra 0.15 after roughing, minimizing the need for secondary finishing.